Automotive Industry Masterclass Insights
.png?width=58&height=58&name=REEJIG_PRIMARYLOGO_SYMBOL_BLUE_RGB%20(1).png)
⏳ This Class in 60 Seconds
AI is transforming the Automotive Industry, driving efficiency, reducing costs, and reshaping workforce roles.
- AI-powered robotics and automation are automating 35–50% of manufacturing processes, cutting labor costs by 20–25%.
- AV Engineers, manufacturing workers, and service technicians are transitioning into high-tech, AI-driven roles.
- Companies that prioritize AI adoption and workforce reskilling today will lead the future of mobility.
1. The Industry Shift: Why AI is Reshaping Automotive
The Automotive Industry is undergoing rapid transformation, fueled by the shift to electric vehicles (EVs), autonomous driving, and connected car technology.
- $3.9 Trillion Market: The global automotive sector was valued at $3.9 trillion in 2023, contributing 5% to global GDP and directly supporting nearly 14 million jobs worldwide.
- 92 Million Vehicles Produced: In 2023, global vehicle production grew by 4.5%, driven by demand in North America, Europe, and China.
- CEO Insight:
- Mary Barra, CEO, General Motors:
"The semiconductor shortage was a wake-up call. We cannot rely on distant supply chains for critical components."
- Mary Barra, CEO, General Motors:
2. AI’s Biggest Workforce Impact Areas (Key Roles & ROI)
AI is transforming the Automotive Industry by automating repetitive processes and creating high-value tech roles. Three high-impact roles stand out:
- Manufacturing Workers
- Impact: AI-powered robotics automate 35–50% of manufacturing tasks, including assembly, logistics, and quality control.
- ROI: Reduces labor costs by 20–25% and improves operational margins.
- Implementation Timeline: 24–36 months for AI-powered RPA and AGV deployment.
- AV Engineers & AI Developers
- Impact: AI in autonomous vehicle (AV) development, testing, and data modeling improves efficiency by 30–40%, reducing development cycles by 25%.
- ROI: Lowers R&D costs and accelerates time-to-market by 12–18 months.
- Implementation Timeline: 6–12 months for AI development system integration.
- Aftermarket Service Technicians
- Impact: AI-assisted diagnostics and predictive maintenance increase service efficiency by 30–40%.
- ROI: AI chatbots reduce customer interactions by 50%, cutting service costs while improving first-time resolution rates by 25%.
- Implementation Timeline: 0–6 months for AI chatbot and remote diagnostics deployment.
3. Reskilling Strategy: Who’s at Risk & Where to Invest
AI is reshaping workforce dynamics in the automotive industry, creating a need for reskilling. Here’s where to focus efforts:
- Internal Combustion Engine (ICE) Mechanics ➡️ EV Maintenance Technician
- Skills Needed: High-voltage system handling, software diagnostics.
- ROI: 80–90% retention, $28,500 ROI per employee, and 30% salary growth.
- Timeline: 6–9 months of training through programs like Ford’s EV Technician Program.
- Assembly Line Workers ➡️ Automation & Robotics Maintenance Specialist
- Skills Needed: AI-driven production tools, robotic process automation (RPA).
- ROI: 75–85% retention, $30,500 ROI per employee, and 35% salary growth.
- Timeline: 12–18 months of training through Siemens’ Mechatronics Systems Certification.
- Administrative Roles ➡️ Data Analyst / Process Automation Specialist
- Skills Needed: Data interpretation, RPA system management.
- ROI: 75–90% retention, $26,000 ROI per employee, and 20% salary growth.
- Timeline: 4–6 months of training through Coursera or General Assembly programs.
4. Implementation Roadmap: AI Adoption Timeline
To effectively transition your workforce and adopt AI solutions, follow this phased approach:
Short-Term (0–6 months):
- Deploy AI-powered chatbots and remote diagnostics for service technicians.
- Upskill administrative staff in RPA and data analytics.
Medium-Term (6–12 months):
- Integrate AI systems for AV development and data modeling.
- Reskill ICE mechanics for EV maintenance roles.
Long-Term (12–36 months):
- Scale AI adoption in manufacturing with robotics and AGVs.
- Train assembly workers in robotics maintenance and AI-driven quality control.
5. Get a Personalized Skills Masterclass
A private, hands-on session with one of our workforce strategists—tailored specifically to your organization. In this session, we’ll help you:
🔹 Analyze Workforce Composition: Identify skill gaps and AI opportunities.
🔹 Assess Operational Efficiency Index (OEI): Measure where automation can improve margins.
🔹 Benchmark Industry AI Potential Index (AIPI): Compare your AI adoption with peers.
✅ Walk away with a clear roadmap to integrate AI into your workforce strategy.
✅ Identify high-impact reskilling opportunities to future-proof your workforce.
💡 Explore all upcoming Skills Masterclass sessions
📩 Book a Personalized Skills Masterclass for Your Organization
📚 Where This Data Comes From
This analysis is based on insights from the Automotive Skills Masterclass, industry reports, and Reejig’s Work Ontology™ dataset, including:
- 130M+ job records spanning 5–7 years.
- 41M unique proprietary and public data points analyzed.
- Millions of tasks mapped to track AI adoption and workforce shifts.
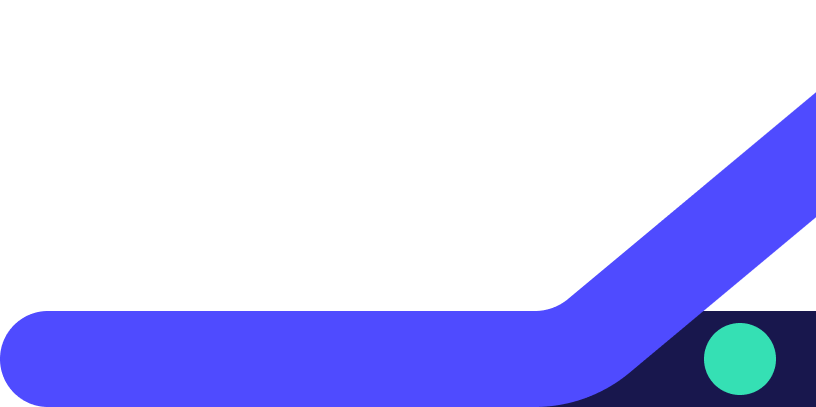